Production d’anodes pour Arvida à l’Usine Grande-Baie : un défi de taille relevé !
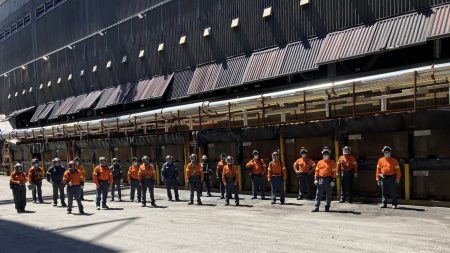
Produire des anodes pour une technologie et des matières premières différentes, le tout dans un format différent. C’est le défi hors du commun qu’ont accepté de réaliser les secteurs du carbone des Usines Arvida et Grande-Baie (UGB) pour pallier un bris sur la presse à anodes de l’Usine Arvida.
Alors que l’Usine Arvida était en augmentation d’ampérage et que tout allait pour le mieux, une importante fissure a été constatée sur le cylindre de la presse à anodes. « Dès que nous avons remarqué le bris, nous avons diminué la pression du cylindre pour maintenir la presse en fonction. Nous avons également monté une équipe de mesures d’urgence pour trouver une solution », explique Kathia Rainville, surveillante de procédé, Usine Arvida.
Comme les commandes à l’externe n’étaient pas disponibles, l’idée d’adapter UGB pour la production d’anodes pour Arvida a émergé. « Personne n’avait réalisé ce défi par le passé, les gens ont eu beaucoup d’audace. Il y a eu beaucoup de collaboration et de partage d’information technique dans toute la région », raconte David Gignac, ingénieur mécanique, Tour à pâte, UGB.
À l’Usine Arvida, les équipes se sont rapidement mises en mode solution. « Ce bris a été un grand casse-tête pour nous. Au début, nous avions approché l’Usine Alma, mais pour des raisons techniques, c’est finalement l’équipe d’UGB qui est venue nous prêter main-forte », explique Lisa Laforte, chef de service Amélioration des affaires.
L’équipe a contacté une usine en Grèce, l’une des seules au monde à produire des anodes doubles, pour obtenir de l’information. Les anodes d’UGB étant approximativement le double de celles d’Arvida, un plan s’est dessiné et ils sont passés à l’action.
Nous avons fait la conception des nouveaux moules à l’interne et c’est Industrie Dodec qui les produits. Il nous fallait trois jours pour reconfigurer la mouleuse #2 d’UGB. Les nouveaux moules nous permettent de produire deux anodes à la fois avec deux matrices, un seul contrepoids, une seule trémie et ce, avec une cadence de 40 anodes à l’heure », ajoute Jacques Guay, technicien mécanique, Scellement des anodes & TMB.
Une adaptation importante a été faite du côté de la main-d’œuvre. L’horaire de la tour à pâte d’UGB, qui est planifié pour 5 jours sur 7, a été modifié pour opérer 7 jours sur 7. Pour accueillir les anodes en surplus, un système de manutention complexe a été mis en place. « À l’aide de conteneurs de refroidissement, munis d’un système de captation des gaz, les anodes Arvida sont entreposées temporairement pour leur permettre de durcir. Le système de filtration a été créé avec du matériel existant et du charbon activé », explique Sylvain Desgagnés, superviseur aux opérations, Tour à pâte, UGB.
Avec une cadence de 7 700 anodes par semaine à UGB, il fallait trouver une façon d’entreposer les 20 000 anodes d’Arvida en plus des 10 000 d’UGB. « Nous avons adapté le champ derrière l’usine pour y accueillir les anodes produites pour Arvida », indique Alain Minier, technicien, Four à cuisson des anodes.
Du côté d’Arvida, le résultat de ce projet inspire beaucoup de fierté : « La synergie entre les équipes d’Arvida, d’UGB et des approvisionnements a été la clé qui nous a permis d’assurer la production d’anodes pour les mois à venir. J’ai vu des gens engagés et déterminés et je remercie sincèrement toutes les personnes impliquées. C’est là qu’on voit la force du travail d’équipe », a tenu à souligner Pascal Therrien, chef de service, Tour à pâte et Scellement, Arvida.
Alors qu’on réalise généralement un projet de 2 millions sur 18 mois, l’agilité des équipes a permis d’effectuer cette transformation en deux mois et demi. Un succès qui restera gravé dans les mémoires de ceux qui ont participé », termine Robin Gilbert, chef de service anodes P155 et maintenant chef de service coulée Laterrière.